Stepping Up with STEM
Local student sparks community effort to create medical face shields
By Nan Bauroth | Photos Courtesy of Charlotte MEDI | Posted on April 7, 2020
Back in 2014, Ballantyne Magazine featured engineering teacher Tom Dubick and his Fab Lab STEM students at Charlotte Latin School in an article titled “The Bright Stuff.”
Now Dubick and his current students have raised more than $100,000 to produce face shields for Charlotte doctors and nurses on the front lines of the COVID-19 battle.
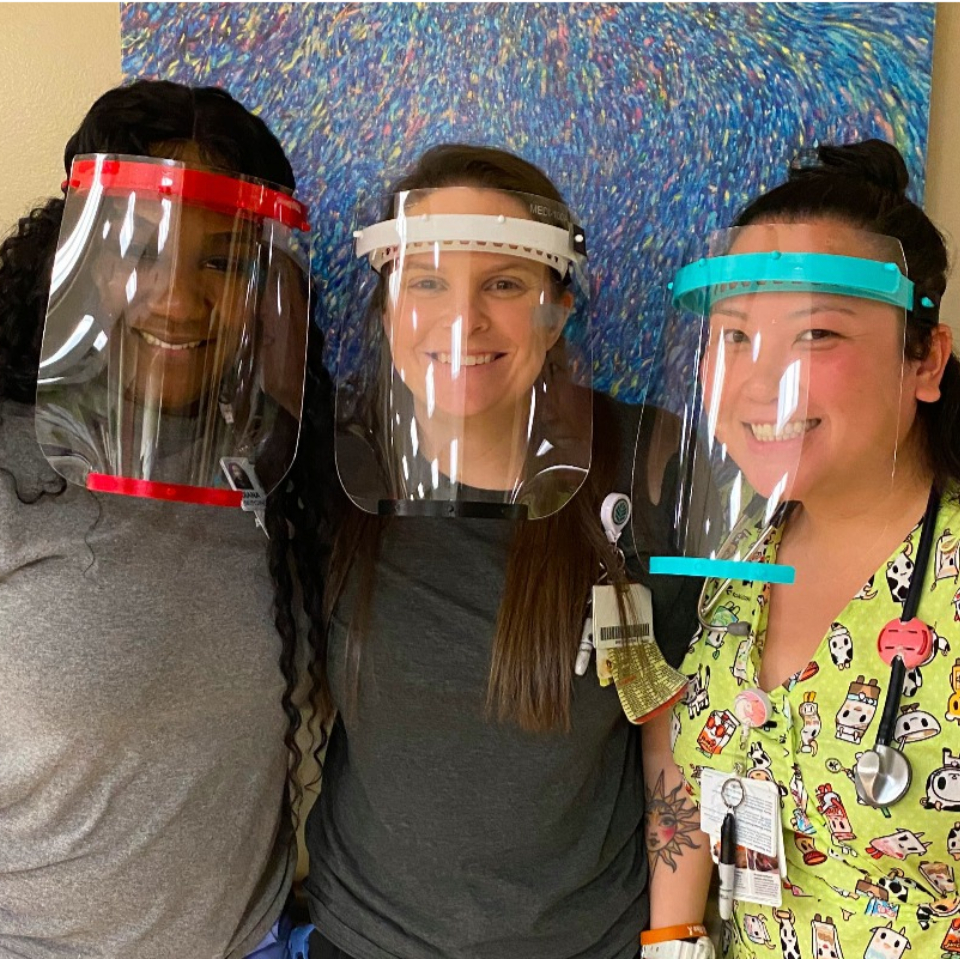
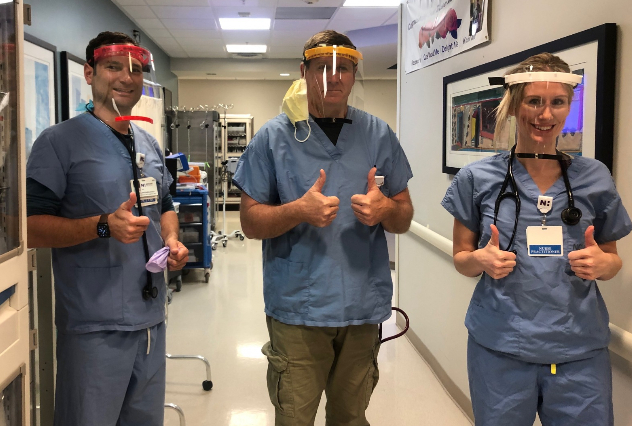
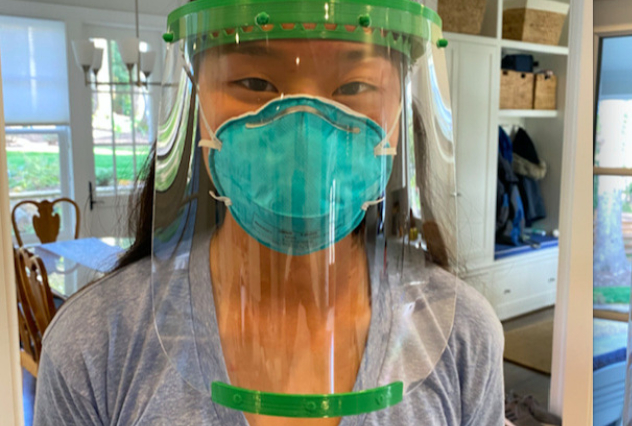
In the first 12 days, the students raced to produce 4,000 face shields on 3D printers. They delivered 100 per day to the ER, ICU, cancer, labor and delivery, anesthesiology and bone marrow transplant centers at the two Atrium local hospital systems, as well as a drive-thru COVID-19 testing center.
Partnering with Terrence Fagan in the department of mechanical engineering and engineering science at UNC Charlotte, the students then formed Charlotte MEDI (Medical Device Emergency Innovation), a nonprofit charged with scaling up production through injection molding. With the help of Texlon Plastic, a local plastics manufacturer, the students hope to produce 50,000 shields per week.
“Your help has been a godsend,” says Stuart Garner, a pulmonary critical care physician at Atrium, speaking of the Charlotte MEDI team. “Thanks to you, my team and the ICU nurses got the shields as the tidal wave of patients were just hitting us. My partners in the ICU Care are, and will remain, very grateful for your team’s help.”
Inspired by a Student
Katie Chai, a junior at Charlotte Latin, sparked the face shield project. She approached Dubick with her concern about insufficient personal protective equipment (PPE) to cover her parents and their health care colleagues. Chai’s father, Seungjean Chai, is an oncologist at Atrium Health and serves as president of the medical staff for Carolinas Medical Center and Atrium Mercy Hospital, as well as director of medical operations for Levine Cancer Institute. Her mother, Janie Chai, is a pediatrician with Novant Health Pediatrics SouthPark.
Dubick, now innovation and design chair at Charlotte Latin, immediately enlisted a “brain trust” of Charlotte engineers, designers and makers to modify an open-source design for face shields and develop a prototype. After consulting local physicians to refine it and ensure their design adhered to CDC standards, the group settled on a clear plastic shield that extends an inch or two in front of the wearer’s nose, leaving enough room to wear a surgical mask underneath. Based on real-time clinical feedback, they began producing face shields by laser cutting a plastic that offer offers chemical splash protection.
“This has been a great community effort with many families, companies and groups coming together,” Dubick says, noting that students at schools all over Charlotte joined to help.
“In only a few weeks, we’ve gone from making four per hour on 3D printers to producing a thousand an hour, and our plan is to keep producing them until the needs of all our hospital, medical and first responders here in Charlotte are met.”
At the time of publication, the Charlotte MEDI team had delivered more than 15,000 shields.
Dubick notes that other Charlotte companies are offering time, resources and services. They include CLT Air Freight Carrier; Bravo Team, an engineering and laser cutting firm; Caro-Polymers, specializing in injection molding; New Wave Acrylics; 2UWaveLaundry; Spangler Packaging Materials and Rubie’s, a manufacturer of elastic headbands.
To donate: charlottemedi.org